RORI is a perfect example of the development work being carried out in the WA mining and resources sector to deliver the workforce of the future.
It’s not human development (although that’s obviously incredibly important – more on it later!). But vital work that aligns with the way operations are constantly looking for ways to solve problems by doing things safer, smarter and cleaner.
RORI, as you might have guessed by now, is a robot. It can climb stairs, travel over rocky terrain and fight fires and its acronym is short for Remote Operated Rescue Initiative.
Most importantly – and a big part of the reason why RORI exists – it can get close to emergency situations that are too risky for humans to attend and report back in real time.
“RORI is equipped with the obvious firefighting capabilities but is also able to provide us with real time data from an incident via in-built gas detection systems, a thermal imaging camera and pan-tilt cameras,” Rio Tinto Business Partner in Health, Safety and Emergency Services and Safety Joel Mowday explained.
“Real time data from the fire ground enables our emergency responders and business resilience team, who are sitting in a safe location outside the exclusion zone, to make strategic decisions on ways to respond to the fire event.
“RORI is also well-equipped to respond to ‘hot tyre’ events, which have been a long-standing challenge for industry. Those events have an exclusion zone of 300 metres due to the potential risks associated with that type of fire to our emergency responders.
“There’s no real [human] response capacity because of that and it often results in significant damage to equipment or total loss of assets due to us not wanting to expose our people to unnecessary risk.
“It’s a problem that’s existed in the industry for an extended period of time and hadn’t been solved…all of a sudden this fit for purpose idea [RORI] pops up that keeps our equipment and assets safe but more importantly keeps our people safe and out of the line of fire.”
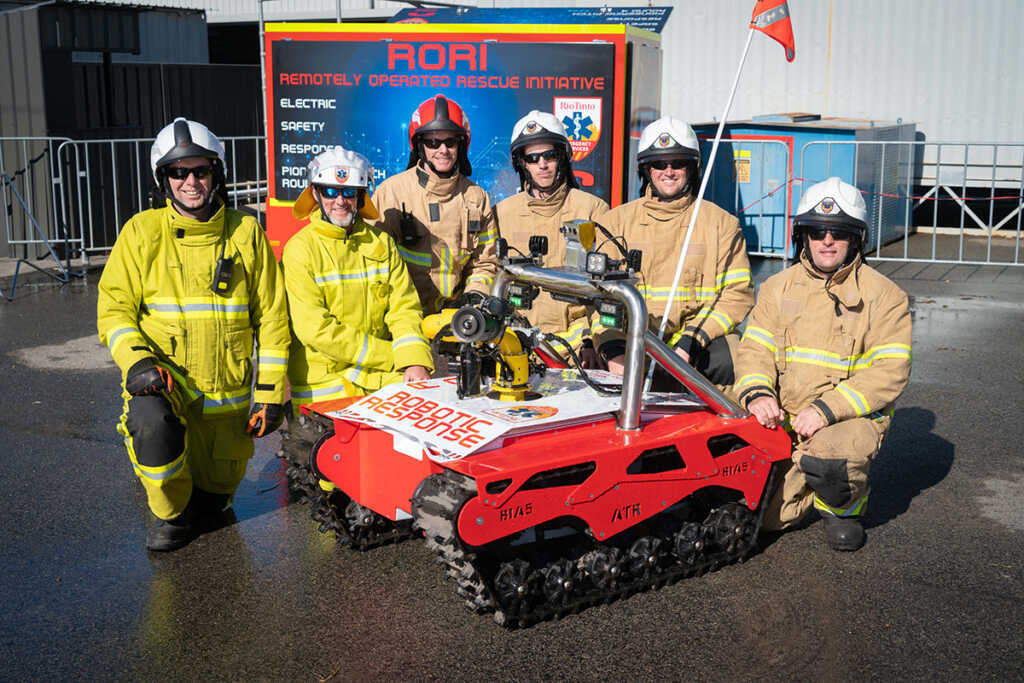
RORI, which is currently undergoing field testing at Rio Tinto’s Greater Brockman operations, is the result of a collaboration between Rio Tinto, Perth-based fire and emergency response supplier InterFire Agencies and robotics expert BIA5.
But its existence can be traced back to Rio Tinto emergency services personnel coming up with an idea, which then found its way into the company’s Pioneering Pitch innovation program.
Automation and robotics are nothing new for Rio Tinto, which launched the world’s first fully autonomous long-distance heavy-haul rail network in mid-2019. Dubbed the “world’s largest robot”, AutoHaul carries iron ore trains up to 2.5 kilometres long and was in 2020 the sole WA finalist for the Sir William Hudson Award, given annually to the best engineering project in the country.
The tech revolutionising WA mine sites
More recently, Rio Tinto opened the Gudai-Darri mine in WA’s Pilbara, billed as its most technologically-advanced to date.
Gudai-Darri, which will be partly powered by Rio Tinto’s first solar farm, has an estimated mine life of 40 years and features autonomous haul trucks, drills and water carts (the latter of which is another world-first) monitored from 1500km away in Perth. Robotics are used in the ore sampling laboratory and to distribute parts in the workshop, while a full digital replica of the processing plant allows teams to monitor and respond to data collected from the plant, and also facilitates interactive 3D virtual training.
In partnership with Caterpillar, Rio Tinto hopes Gudai-Darri will be home to a first-ever operational deployment of zero-emission autonomous haul trucks.
Gudai-Darri provides a fascinating microcosm of the innovation that is taking place right across the WA mining and resources sector.
In 2022, mining company Mineral Resources revealed significant milestone for the autonomous road-train project it is undertaking with automation specialists Hexagon.
The successful testing of the technology on private haulage roads at Mineral Resources’ Yilgarn operations involved three triple-trailer road trains each carrying loads of 300 tonnes.
Only the lead road train in the platoon requires a driver in the cabin.
Mineral Resources’ Chief Executive – Mining Services Mike Grey said the autonomous haulage solution removed safety risks associated with driver fatigue, had the ability to seamlessly service a variety of satellite pits that might shift over time (a challenge for more traditional rail haulage) and could potentially unlock deposits that would previously have been considered economically unviable.
“It’s an extremely proud moment to see our autonomous project grow from desktop concept to iron ore reality so quickly,” Grey said.
“As we get ready for the Ashburton Hub Iron Ore Project and look to unlock stranded tonnes of iron ore, our autonomous road trains will be the vital link between the pit and the port.
“As the first of its kind in the world, it opens up new opportunities for us, as we can trial the technology ourselves before offering it to our Tier 1 customers.”
Hexagon is also the Australian installer of Guardvant technology that is used to monitor driver fatigue and enhance the safety of workers operating machinery that frequently weigh in the hundreds of tonnes when loaded up and which are often worth millions of dollars.
Collie-based Premier Coal introduced the Guardvant system to on-site machinery in 2020 in recognition of the problems posed by fatigue during night and 12-hour shifts.
“A camera sits on the dash continually looking at the operator and that camera has its own algorithms,” Premier Coal Health and Safety Advisor Jamie Wood said.
“It looks for set points of eye moment, head movement and general body movement throughout the whole shift and then has set points for different triggers.
“For things like eye closure and distraction events, or if the operator is looking away for a period of times, it will send them an alert to wake them up or to remind them to look forward.”
All Guardvant data is monitored in real time at the company’s headquarters in Arizona. Incidents are assessed in terms of their severity and for repeated patterns of behaviour, with resulting reports giving the Premier health and safety team the context and details they need to address any long-term issues – including previously undiagnosed sleep issues.
Sometimes technology doesn’t actually have to be on-site to deliver safety benefits, with the increasing use of augmented reality and virtual reality in training technology a case in point.
You don’t have to be on site to learn on the job
Perth-headquartered software development company Sentient specialises in providing training, visualision and automation solutions for mining and resources operators around the world.
Craig Mitchell, a former structural engineer who is now an augmented reality developer at Sentient, said there were obvious benefits in being able to learn key tasks in a digital environment that replicates conditions on-site.
“By placing people in a virtual environment where they can carry out potentially dangerous and complex tasks, they have the ability through VR scenario training to repeat those procedures safely over and over again,” Mitchell said.
“Not only do they feel like they retain the information better, they feel more confident when they actually go out and do it on site.”
In other instances, automation and technology is driving both safety and efficiency improvements at operations.
After Fortescue Mining Group realised its Christmas Creek mobile maintenance crew was having to make 12,000 separate 28-kilometre round trips each year to collect equipment and parts, the iron ore miner collaborated with Ford on a bespoke solution.
The result was four Ranger utes retrofitted with on-board automation systems that enable driverless equipment transfers and free up team members to devote more time to maintenance work.
The systems incorporate Radar/Lidar (light detection and ranging) technology that facilitates obstacle detection and avoidance, an independent safety management and fail-safe braking system, and built-in system monitoring and fault response capability.
“With the flexibility to introduce similar systems into other mobile assets, this project is fundamental to our future mobile equipment automation projects,” FMG Chief Executive Elizabeth Gaines said.
Technology helps shape the workforce of today…and tomorrow
One of the questions that often arises around the increased use of technology in any industry is whether it will lead to reductions in human workforces.
But WA mining and resources had a record 156,000 employees in 2021 and, with $156 billion of projects in the State’s pipeline, the aim is that the sector will provide employment for more people – not less!
As Mineral Resources’ Grey noted in relation to the autonomous road train project, unlocking ore bodies that weren’t previously considered economically viable to mine will lead to the creation of more jobs.
And then there are the jobs of the future that will focus on new technology being introduced at operations.
In 2020, Curtin University’s WA School of Mines appointed FMG executive Dr Robert Solomon as its inaugural Professor of Practice in Mining Automation and Data Analysis, to help prepare future generations of mining professionals for careers that will involve as much data as digging.
Meanwhile, the Chamber of Minerals and Energy of WA is forging ahead with a program aimed at introducing WA schoolchildren to the skills needed to be part of the sector’s workforce of the future.
Designed in collaboration with leading mining and resources companies and computer science education specialist Grok Academy, the Digital Technologies Program was successfully piloted in Pilbara schools in 2020. With encouragement from the WA Government, it’s now ready to be rolled out more widely and teach youngsters across the State the foundations of robotics and coding.
Research commissioned by the Minerals Council of Australia and undertaken by EY shows clearly why that knowledge will be needed.
The Skills Map for the Future of Work report published in 2019 found that technology and innovation would significantly alter the viability of potential mining projects and provide people with more valuable employment opportunities.
But it also identified that 35 per cent of mining jobs would be redesigned and upskilled over the next five years, highlighting the need for all levels of education to develop ‘future workers’ whose skills align with those required by industry.
To find out more about how the WA mining and resources sector is innovating now and for the future, visit safersmartercleaner.com.au